Production
Our Production skills in figures:
· 11 million parts of production capacity per year
· 10 million components handled during the year in the industrial warehouse
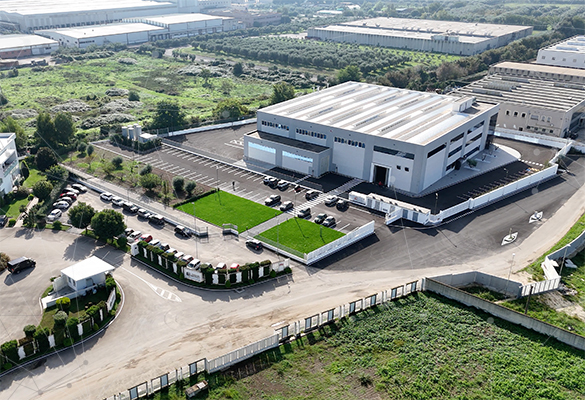
Plant 2 - Industry 4.0
A new manufacturing plant
The expansion of Original Birth’s industrial complex, which now covers approximately 60,000 square meters, marks a significant step toward greater efficiency and integration of production processes.
The new factory section, designed according to Lean Manufacturing principles, houses advanced departments for mold design and construction. Here, technologies such as the injection-blow molding system and dual-station MIG welding robots enable the complete in-house management of the entire production cycle, from design to the creation of the finished product.
Innovation, technology, and sustainability
The plant has been reorganized with a 4.0 approach, featuring full digital interconnection that reduces the time-to-market for new projects and speeds up order fulfillment. This integrated approach combines Smart Production, Smart Service, and Smart Energy, ensuring flexibility and fast decision-making processes.
The excellence of Made in Italy
In an industry that often relocates production abroad, Original Birth goes against the trend, reaffirming its Italian identity through strategic choices focused on quality and sustainability. Every stage of the process, from the chemical analysis of materials using high-tech spectrometers to the creation of the necessary tools for spare parts, reflects a constant commitment to excellence.
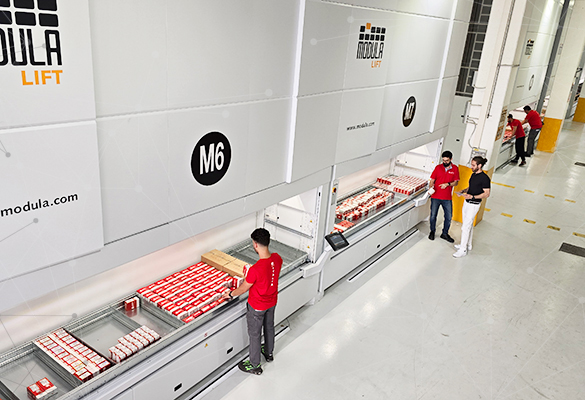
Logistics and automated warehouses
Adoption of automated warehouses: Modula Lift
To meet an increasingly diverse demand, the company has invested in modernizing its logistics. Advanced product code management and optimized workflow organization ensure agility in meeting the needs of a demanding and dynamic clientele.
A key role is played by automated warehouses and advanced management software, which optimize both logistics and production flows. This investment, part of a now-completed three-year plan, not only increases production capacity but also strengthens the company’s competitive positioning.
These systems achieve a total load capacity of approximately 90,000 kg—an innovation that simplifies and optimizes workflow, allowing for the storage of 4,500 product codes with a four-month stock supply for each code.
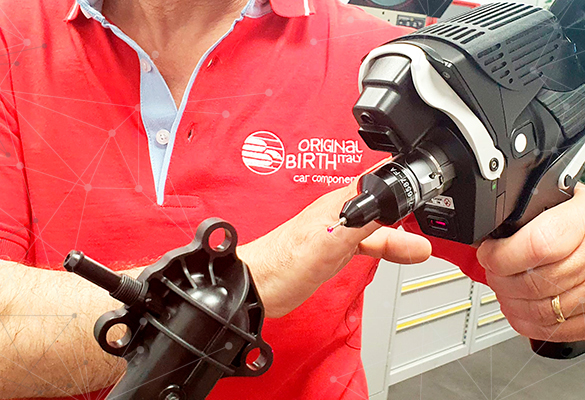
Moulding design
The design of a mold is carried out using reverse engineering techniques. The original product sample is taken, scanned, and the so-called "point cloud" is acquired. After modeling the geometric solid, the mold is designed. Once the design phase is complete, CAD simulations of the mold are performed, and construction is authorized.
Use of the most advanced modern technologies:
- Three-dimensional measurements – 3D
- Reverse Engineering
- High-speed point-to-point laser scanning
- Measurement precision certified according to ISO 10360-12
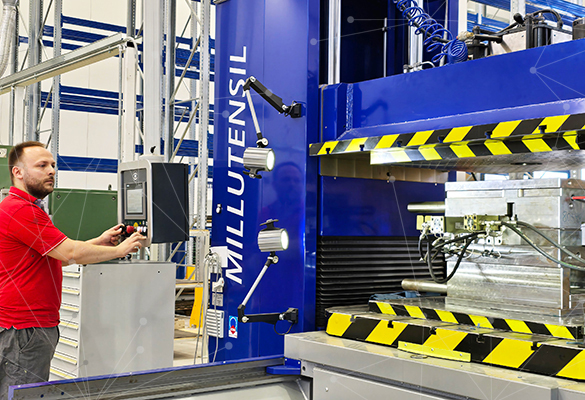
Tool area
Once the mold is constructed, it is tested using a mold testing press. The machine simulates the operation of the product by running the same production cycle that will be used in manufacturing: injection, mold opening, movements, and extraction.
The mold testing ensures 99% functionality, minimizing production downtime and increasing productivity.
Use of the most advanced modern technology:
-
Millutensil mold testing press
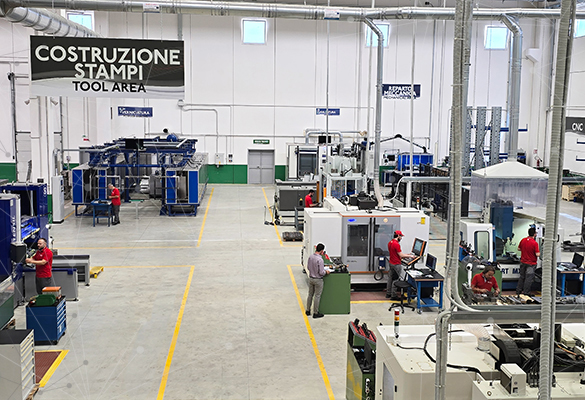
Industrial design
The tooling department is equipped with state-of-the-art CNC machining centers, all of the latest generation. These machines, combined with the technical and industrial expertise of our specialists, are an invaluable resource for Original Birth and its ongoing development.
Molds and fixtures for assembly, production, and product control are designed with high-precision mechanical machining..
Production Capabilities:
- CCNC machining centers ranging from 0 to 1400 mm
- Wire cutting up to 800 x 550 x 510 mm / Speed 3000 mm/min
- Surface grinding up to 800 x 400 mm
- Cylindrical grinding up to 120 x 400 mm
- Spark erosion with a maximum size of 800 x 600 x 450 mm
Maximum mold dimensions: 1000 mm x 800 mm
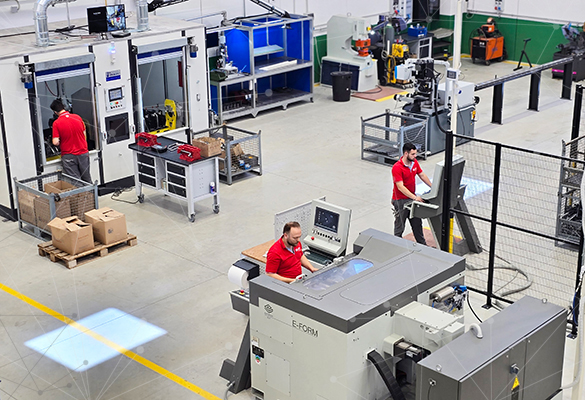
Mechanical Engineering
The mechanical department is equipped with cutting-edge technologies that enable the production of cooling water tubes and more.
It has fully electric bending and shaping machines that, through software, simulate the deformation process, generating the technological processing cycle. The department also includes a dual-station MIG welding robot. This robot ensures precision and consistent repeatability, minimizing waste, defects, and maximizing productivity.
- Robotic welding
- Machining center
- Tube bending machine
- Tube shaping machine.
- Pickling and powder coating system.
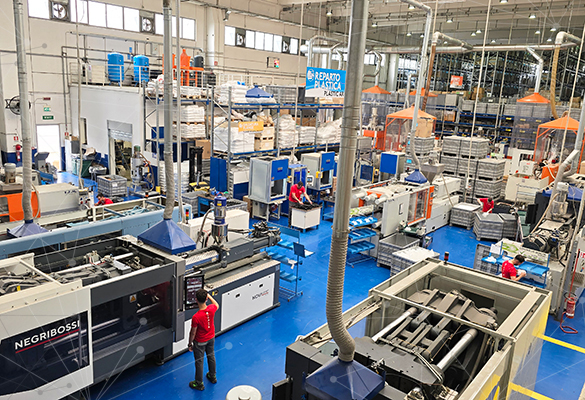
Production of plastic components
The use of state-of-the-art injection molding presses, combined with the expertise of our technicians, ensures the high quality of our plastic and thermoplastic products.
Original Birth offers a full range of water tanks available throughout Europe.
The extensive production of thermostatic flanges and distribution filters is one of the most significant in the industry, with welding performed using hot blade, ultrasonic, and vibration techniques.
· Welding machines: vibration, ultrasonic, and two hot blade rotofriction units – with test machines
Production Capacity:
4.5 MILLION PIECES PER YEAR
· Press weight ranges from 50 to 500 tons
· Minimum processing capacity: 270 mm x 270 mm
· Maximum processing capacity: 900 mm x 800 mm
· Maximum mold opening: 900 mm
· Production capacity in PS from 10 to 1800 g
· Injection Molding Press
· Raw materials used: PVC, PA6, PA6T6IFV, PA6MD, PA66, PA66FV, TPV, PBT, PP, PPS, PPFV, PE, ABS, PUR, PS, TPC-ET, POM.
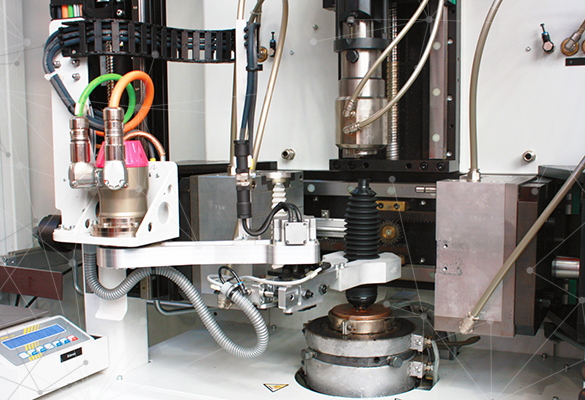
Rubber Production
Modern thermo-hydraulic injection and blower presses enable the production of rubber and rubber-to-metal parts.
Original Birth owns its own design for rubber boots.
Production Capacity:
3 MILLION PARTS PER YEAR
- Press Tonnage from 180 up to 400TN
- Minimum size capacity for toolings 550 mm x 550 mm
- Maximum size capacity for toolings 700 mm x 700 mm
- Main raw material emplyed: SBR, NBR7060, NBR12570/90, NBR50, H-NBR, EPDM65/55, CR, GOMMA NATURALE 75/70/65/60/55.
PRODUCTION OF THERMOPLASTIC BOOTS: Pressblower DSEI 50
Production Capacity:
1.7 MILLION PARTS PER YEAR
- Minimum size capacity 50 gr
- Maximum size capacity 2500 gr
- Main raw material emplyed: TPC-ET, TPV, TPU.

Assembly Lines
Strategic collaboration with highly qualified partners, along with the transfer of our own technology and know-how, allow Original Birth to develop, produce and assembly a wide range of critical and safety components.
Critical components such as silentblocks, fully produced by Original Birth or OE manufacturers, are assemblied into our suspension arms and stabilizer bars, giving an added value to this range.
Production Capacity:
- From 1.000 up to 5.000 pcs a day pcs a day
- Laser markings from 1.000 up to 10.000 pcs a day
- 2 silent block press fitting machines
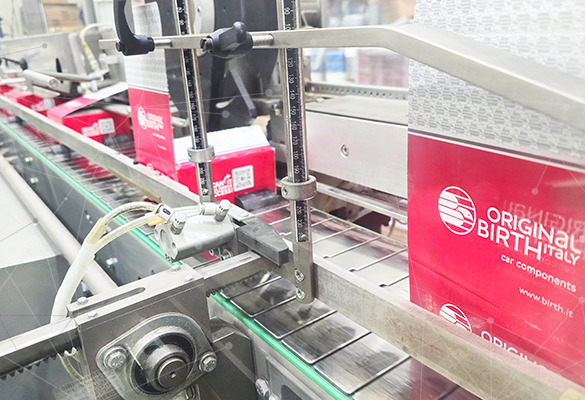
Packaging
An automatic packaging line help us to be fast in filling, day by day, our stock of Finished Products. Thanks to the use of Automated machines, we are able to pack thousands of products in boxes and bags every day.
Packaging Capacity:
- IMBALL: more than 8.000 pcs a day
- TECNOPACK: more than 7.000 pcs a day
- Boxing machine with oscillating arm for label application
- Kit packaging machine
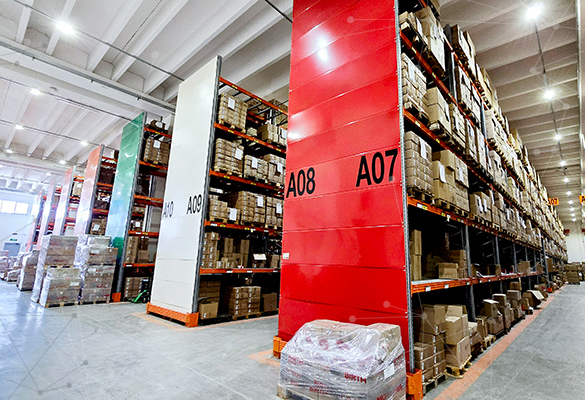
Warehouse
- ABCD Warehousing stock rotation
- 1.800 industrial crates
- more than 20.000 pallet places
- 15.000 active picking positions
- Modula automatic warehouses

Private Label
Our quality at your service
Our private label service combined with a marking laser system of the latest generation, make us the ideal partner for your customisation needs.
Company single member company subject to the management and coordination of Emera S.p.A.